In this article we will talk about the most important aspect for Macsa in managing an appropriate quality control system, guaranteeing top product performance and total customer satisfaction.
Quality Control; guaranteeing exceptional service
What are the quality processes for our products?
1. Design quality
When our R&D department designs the products that we go on to manufacture, two aspects about final quality are focused on:
- The quality of the components: Macsa ID engineers focus their efforts on designing and developing everything that gives us added value and sets us apart from the competition. On the other hand, for all components of little added value, Macsa prioritizes the use of verified brands and with approved certifications (either UL or ETL) providing unshakable product quality.
- The design of the manufacturing processes: to achieve a quality finished product, it is necessary to define the different production processes and to ensure the manufacturing process guarantees finished product quality.
- The manufacturing processes are thoroughly analyzed. In these processes, the Quality Department anticipates possible defects that may arise and ensures that the fundamental design process principles are implemented.
2. Supplier quality
In order to guarantee quality manufacturing and the required product lead time, we carry out requirement checks for all our main suppliers, ensuring that the quality of the products delivered to Macsa is optimal. Supplier standardization is a key aspect in guaranteeing top quality and service. We evaluate each of our key suppliers on a quarterly basis with our Supplier Evaluation system, identifying incidents detected in the plant and deviations in delivery deadlines.
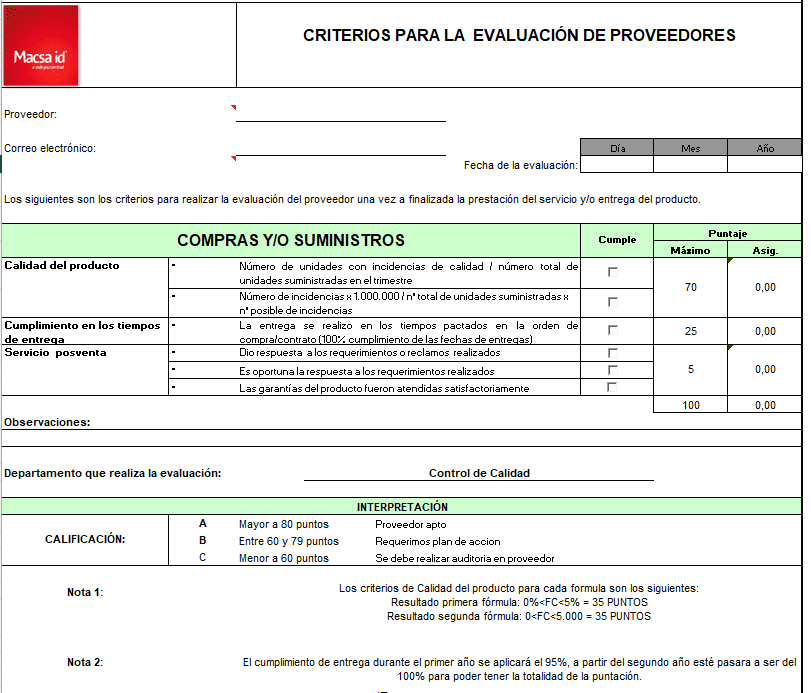
Here is a list of some of the different types of supplier we work with at Macsa:
- Laser tubes
- Scanners
- Optics
- Machining
- Mechanics
- Wiring
- Electronics
- Painting and anodizing
- High resolution heads
- Printing engines…
In addition to the verified quality required for most of the products, our Quality Department performs an important check in order to guarantee the high level of excellence demanded by the market. Incoming materials that are identified in our system as critical are thoroughly checked, thus allowing us to detect possible problems before the product enters our production lines.
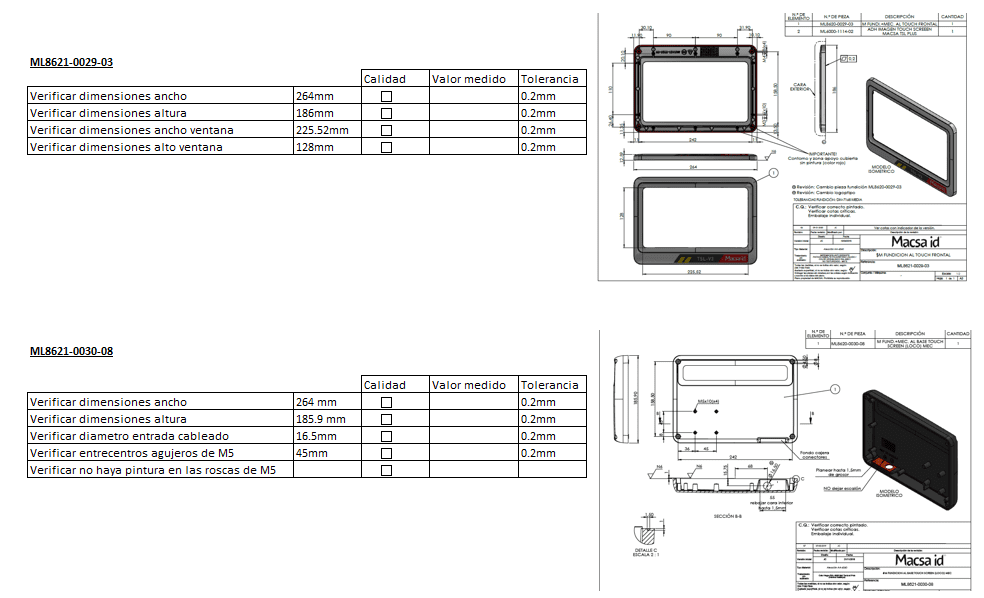
All quality incidents detected in our system generate a Non-Conformity, where an 8D report is required from our suppliers in order to analyze the root cause of the problem and to define corrective and preventive actions to avoid a future repetition of the incident.
3. Manufacturing quality
So as to guarantee the correct assembly and setup of all our equipment, different check points are deployed during the various manufacturing stages. Each machine model has its own verification check, where the key points to be taken into account are specified to guarantee optimum assembly and operation. This allows us to validate each of our machines during the different production phases, avoiding factory setbacks. Once the production process is finished, our Quality Department verifies all the equipment individually. Each model has a specific verification document which indicates the critical points to be verified.
The following are some of the tests performed on the different equipment:
- Specific verifications for each machine on the assembly and adjustment line.

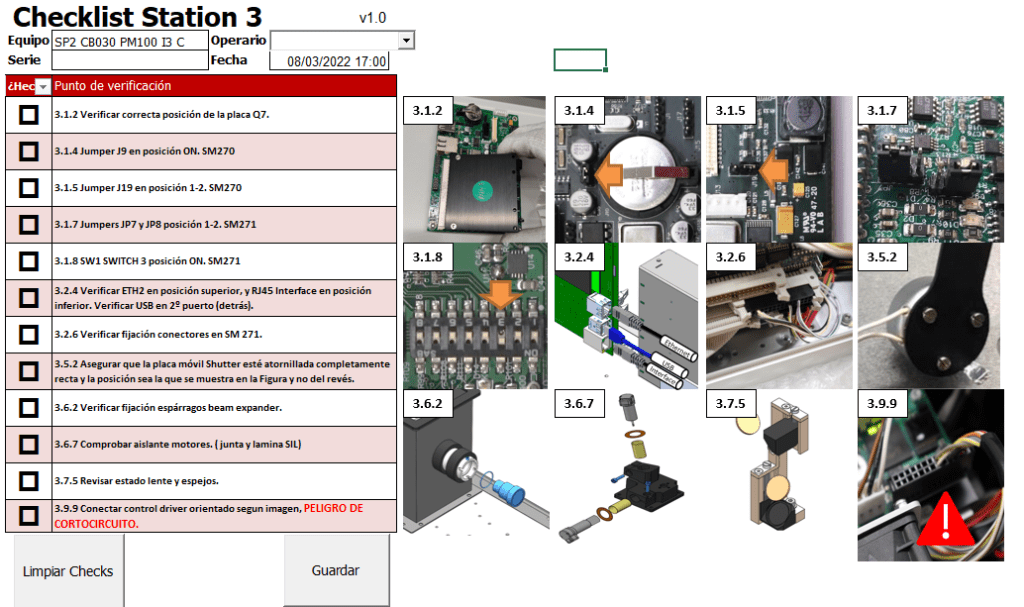
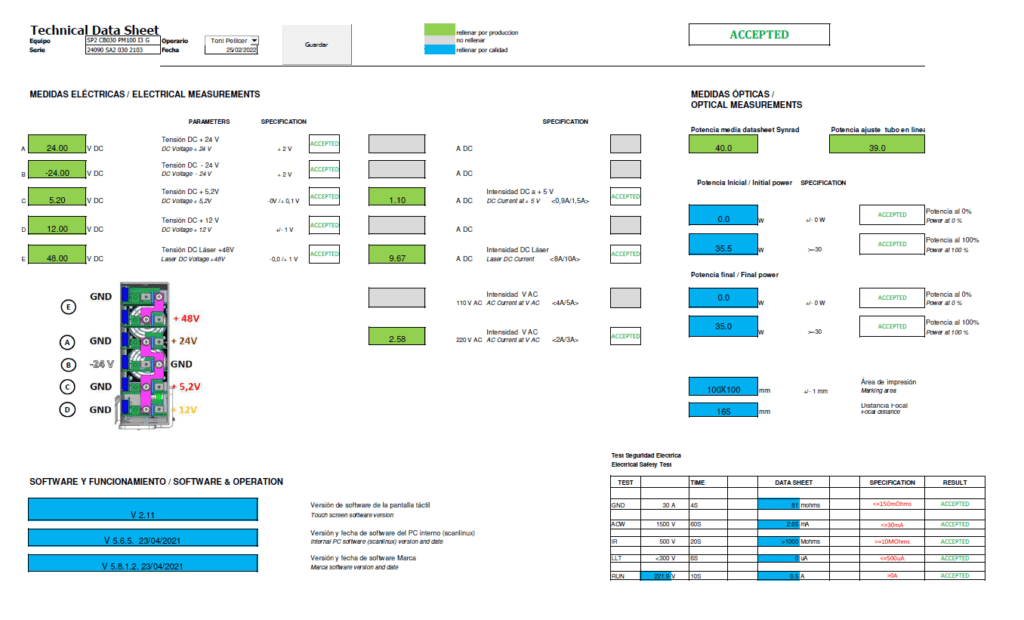
- Functional test of all equipment (I/O signals, photocell test, encoder test, ethernet, touch screen…).
- Marking test at different printing speeds.
- Electrical safety test of all equipment.
- Marking test of +12 hours on each laser (hot and cold power measurements of each laser tube).
- Verify customer specifications (special specifications are verified for each installation, ensuring that the equipment manufactured meets our customer requirements).
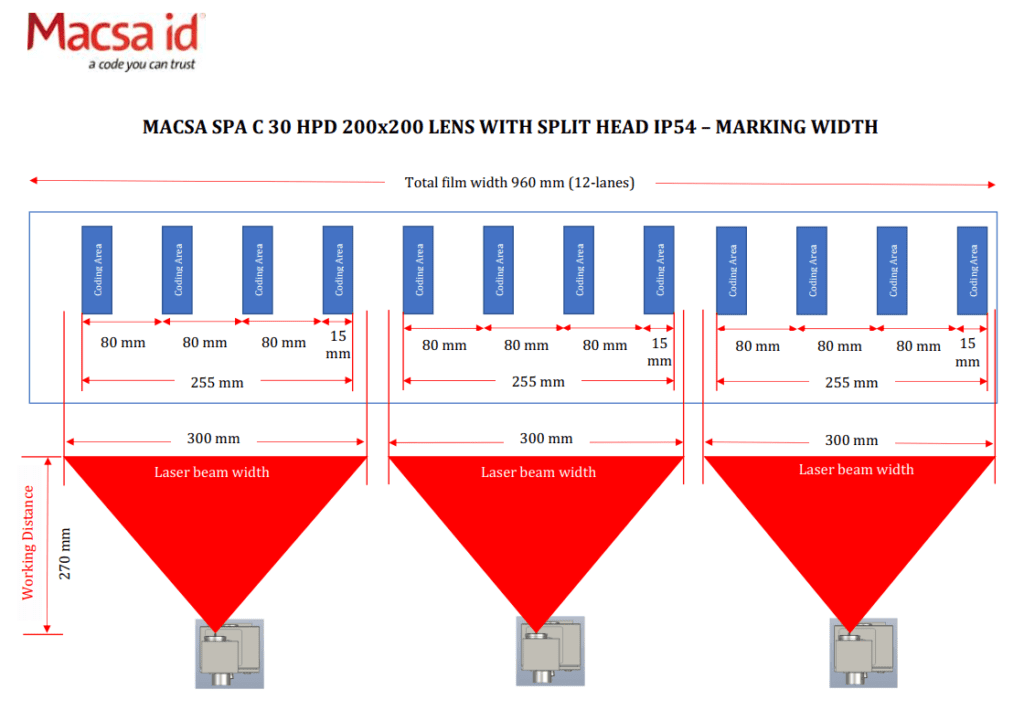
- Labeling test on P&A equipment (tests are performed with the customer labels or equivalent labels to always guarantee the desired application).
- Continuous printing test on Inkjet equipment, ink checks of all machines to ensure proper operation.
- Software validation (each new software version is verified).
- Laser equipment software.
- Touch screen software.
- Inkjet equipment software.
- P&A equipment software.
4. Shipping quality
All of the above processes would be meaningless without without proper packaging of our products. Our main objective is to be able to reach all parts of the world and to ensure that all our products arrive in perfect condition. For this, it is essential to have good packaging design that allows us to work with the different modes of transport (sea, air, land, train).
- Specific packaging for each machine model (laser, inkjet, P&A)
- Special packaging for maritime shipments.
- Packaging for special spare parts (optics, electronics, laser tubes…).
- Packaging of special projects.
If you are looking for the best laser solution, do not hesitate to contact us: